Fish feed manufacturing process
How do you manufacture fish feed? The fish feed manufacturing process combines scientific knowledge, technological innovation, and quality focus. Beyond production, it aligns biology, engineering, and nutrition for an optimal product. Making fish feed involves understanding nutritional needs, requiring research and collaboration among biologists, nutritionists, and experts to fulfill specific nutrient requirements for different fish life stages.
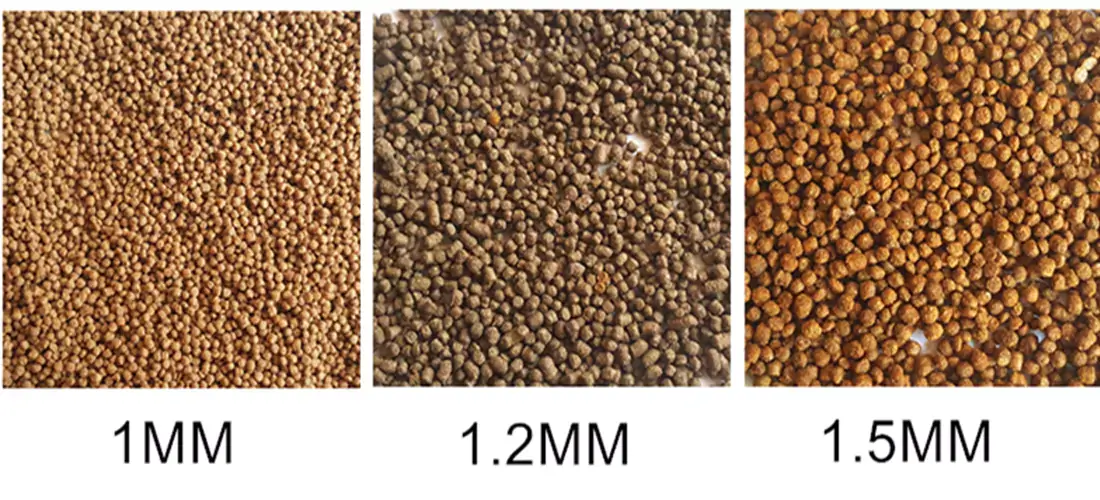
Technology plays a vital role in the fish feed manufacturing process. From the initial grinding of raw materials to the precise extrusion and coating technologies, state-of-the-art machinery is employed. These technological advancements enable manufacturers to achieve consistent quality, uniform pellet size, and various pellet shapes. They also enhance production efficiency, allowing large-scale production that meets the ever-growing global demand. you can setup a small fish feed plant with the below equipments to manufacture fish feed.
video of how to manufacture fish feed
Ingredient Selection and Quality Control when you manufacture fish feed:
- Sourcing: Engage with global suppliers following strict quality standards, sourcing fish meal, grains, vitamins, minerals, and oilseeds ethically.
- Inspection: Use advanced lab techniques to analyze fish feed raw materials for nutrient composition, moisture, ensuring compliance with international standards.
the process of How do you manufacture fish feed
Grinding:
- Hammer Mills: when you manufacture fish feed, use advanced grinders for fish feed powder, for digestibility to fish nutritional needs.
Mixing:
- Batch Mixers: Utilizing highly sophisticated mixers that employ both rotation and agitation, operated under precise timings and speed configurations. This ensures an optimal blend of vitamins, proteins, fats, and other nutrients, fostering a consistent nutritional profile across each pellet batch.
Conditioning:
- Steam Conditioner: Implementing technologically advanced steam conditioners when you manufacture fish feed that uniformly introduce moisture and heat. This initiates starch gelatinization, enhances protein denaturation, and leads to improved pellet texture and nutritional integrity.
Extrusion:
- Extruder Types: Operating specialized single screw floating fish feed pellet machine and twin screw extruders configured with specific screw geometry, temperature, and pressure settings. These factors collectively govern the cooking process, leading to well-formed pellets. floating fish feed extruder is the most important step in how do you manufacture fish feed.
- Shaping Die: Design custom dies for pellets in sizes and shapes to fit fish mouth types, aiding efficient feeding.
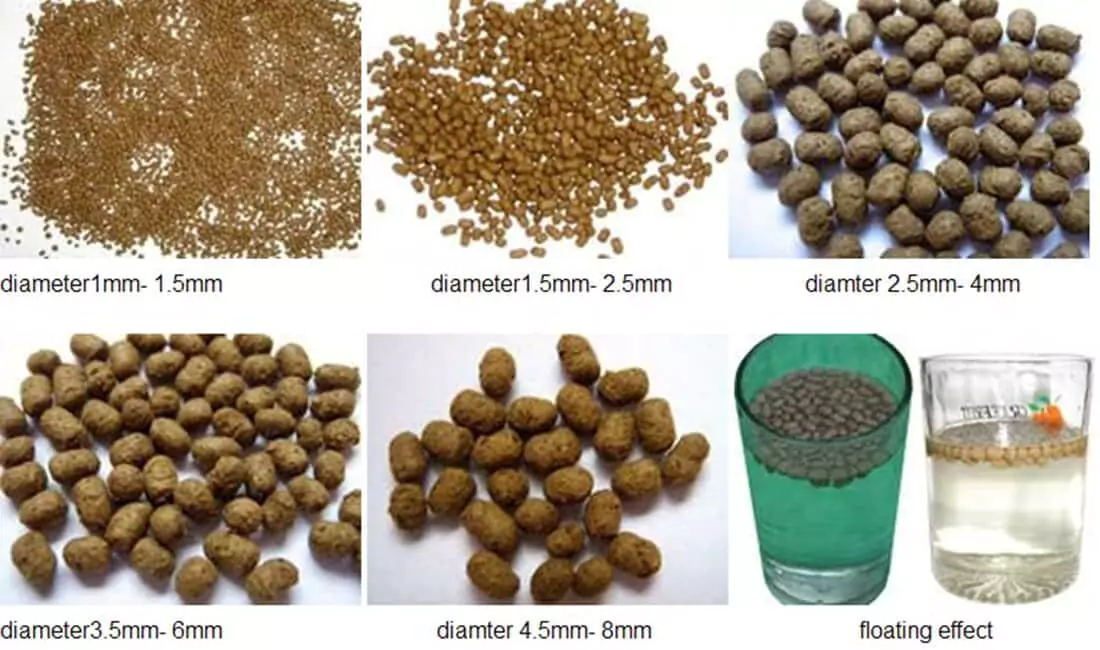
Cutting:
- Rotating Knives: when you manufacture fish feed, utilizing precisely calibrated rotating knives that ensure uniform cutting of the pellets. This stage requires expert alignment to guarantee consistent pellet length, optimizing feeding efficiency and reducing waste.
Drying and Cooling:
- Conveyor Dryer: Use multilevel conveyor dryers to reduce moisture with controlled temperature and airflow, preserving pellet integrity and shelf life.
- Counterflow Cooler: Implement systematic cooling with counterflow coolers using controlled airflow for even cooling and minimal temperature stress on pellets.
Coating:
- Spray Coaters: Integrating state-of-the-art spray systems that uniformly apply essential oils, flavors, pigments, or micro-nutrients on the pellet surface. This process when you manufacture fish feed enhances visual appeal, taste, and specific nutritional characteristics, meeting varied fish preferences.
Sieving:
- Vibratory Sieves: Use precise sieving machines that filter pellets by size with vibratory motion, ensuring uniform quality.
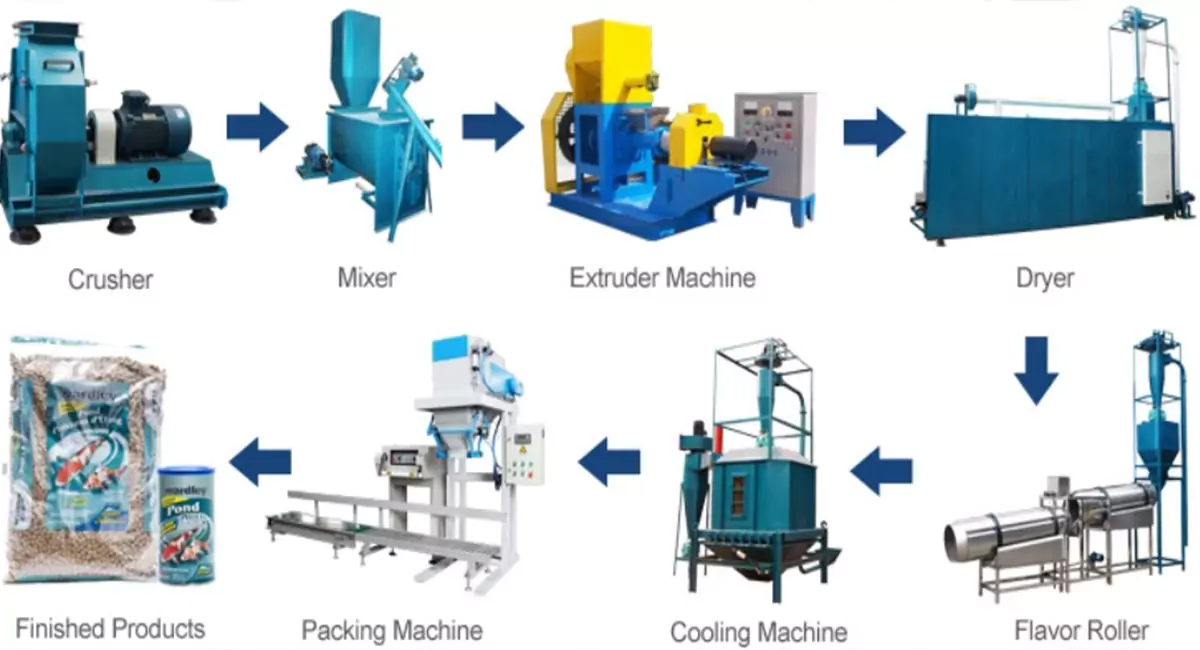
Packaging:
- Automatic Bagging Machines: Automatic Bagging Machines: Utilize automated lines for precision weighing, filling, sealing, and labeling during fish feed production. Advanced sensors and controls preserve freshness and facilitate efficient transportation and handling.
- Labeling: Ensure labels contain ingredient lists, nutritional information, storage instructions, meeting all legal standards when you manufacture fish feed.
Quality Assurance and Distribution when you manufacture fish feed:
- Final Testing: Conducting thorough lab tests by certified experts to verify nutrient content, texture, and durability using advanced equipment.
- Storage and Distribution: when you manufacture fish feed, Implementing temperature-controlled storage and efficient logistics for fish feed, maintaining quality.
FAQs About Fish Feed Production and Usage
Is Homemade Fish Feed a Viable Alternative to Commercial Feed?
Homemade fish feed can be a viable alternative for small-scale farmers or hobbyists. It allows for control over the ingredients and can be cost-effective. However, it requires knowledge of fish nutrition to ensure the feed meets all the dietary needs of the fish.
How Important is Pellet Size in Fish Feed?
Pellet size is crucial when you manufacture fish feed as it needs to match the size of the fish mouth. Smaller fish require finer, smaller pellets to facilitate easy consumption and digestion, while larger fish can handle bigger pellets. Proper pellet size ensures efficient feed utilization and growth.
Can Fish Feed Affect Water Quality?
Yes, fish feed can significantly affect water quality. Overfeeding or using low-quality feed can result in uneaten feed accumulating in the water, leading to increased ammonia levels and decreased oxygen levels, which can harm fish health.
How Long Does Fish Feed Last Before It Expires?
The shelf life of fish feed varies by product and storage conditions but generally ranges from 6 to 12 months. It’s essential to store fish feed in a cool, dry place when you manufacture fish feed, away from direct sunlight to preserve its nutritional quality and prevent spoilage.
What Are the Benefits of Extruded Fish Feed Over Pelleted Feed?
Extruded fish feed, which is processed at higher temperatures and pressures than pelleted feed, offers several benefits, including higher digestibility, better nutrient retention, and the ability to float on water, which makes it easier to monitor consumption and reduce waste.
How Do You Determine the Right Amount of Feed for Fish?
The right amount of feed depends on various factors, including fish species, size, water temperature, and the feed’s nutritional content. Generally, fish should be fed 1-3% of their body weight daily, divided into multiple feedings. Observing fish behavior and appetite can help adjust feeding rates.